The Single Strategy To Use For Turbochargers
Table of ContentsIndicators on Turbochargers You Need To KnowThe Best Guide To TurbochargersTurbochargers - An Overview
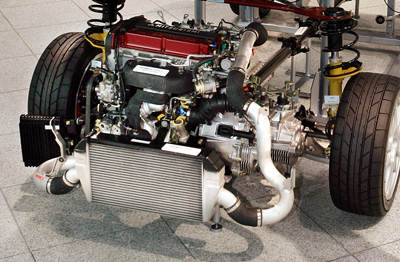
For instance, in Opel bi-turbo Diesel, only the smaller turbocharger works at low speed, supplying high torque at 1,5001,700 rpm - turbochargers. Both turbochargers operate together in mid range, with the smaller sized one pre-compressing the air, which the larger one further compresses. A bypass valve controls the exhaust circulation to each turbocharger.
Smaller sized turbochargers have less turbo lag than larger ones, so frequently 2 little turbochargers are utilized rather of one large one. This configuration is popular in engines over 2. 5-litres and in V-shape or fighter engines. Twin-scroll or divided turbochargers have 2 exhaust gas inlets and 2 nozzles, a smaller sized sharper angled one for quick reaction and a bigger less angled one for peak efficiency.
In twin-scroll designs, the exhaust manifold physically separates the channels for cylinders that can disrupt each other, so that the pulsating exhaust gasses circulation through different spirals (scrolls). With common firing order 1342, 2 scrolls of unequal length pair cylinders 1 and 4, and 3 and 2. This lets the engine efficiently utilize exhaust scavenging strategies, which reduces exhaust gas temperature levels and emissions, enhances turbine effectiveness, and lowers turbo lag obvious at low engine speeds.
The vanes are positioned simply in front of the turbine like a set of a little overlapping walls. Their angle is changed by an actuator to obstruct or increase air circulation to the turbine. This variability keeps a similar exhaust speed and back pressure throughout the engine's rev range. The result is that the turbocharger enhances fuel efficiency without an obvious level of turbocharger lag.
The compressor is comprised of an impeller, a diffuser and a volute real estate. The operating variety of a compressor is described by the "compressor map". The flow variety of a turbocharger compressor can be increased by permitting air to bleed from a ring of holes or a circular groove around the compressor at a point somewhat downstream of the compressor inlet (however far nearer to the inlet than to the outlet).
The 5-Second Trick For Turbochargers
It accomplishes this by requiring a simulation of impeller stall to take place next continually. Enabling some air to get away at this location inhibits the start of rise and widens the operating range. While peak efficiencies might reduce, high effectiveness may be achieved over a greater series of engine speeds. Increases in compressor effectiveness result in slightly cooler (more dense) intake air, which enhances power.
The capability of the compressor to offer high increase at low rpm may also be increased partially (because near choke conditions the compressor draws air inward through the bleed course). Ported shrouds are utilized by numerous turbocharger makers. The centre hub turning assembly (CHRA) houses the shaft that links the compressor impeller and turbine.
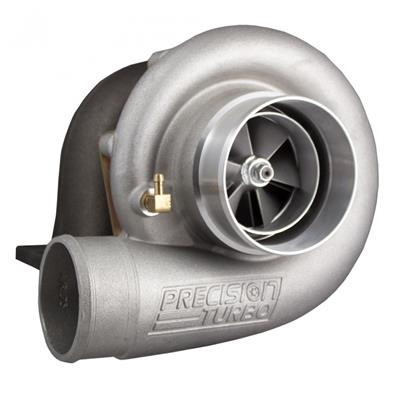
Ball bearings designed to support high speeds and temperature levels are in some cases used rather of fluid bearings to support the turbine shaft. This assists the turbocharger accelerate more quickly and reduces turbo lag. Some variable nozzle turbochargers utilize a rotary electric actuator, which utilizes a direct stepper motor to open and close the vanes, instead of pneumatic controllers that run based upon air pressure.
When the pressure of the engine's consumption air is increased, its temperature likewise increases. This occurrence can be explained through Gay-Lussac's law, specifying that the pressure of an offered amount of gas held at constant volume is straight proportional to the Kelvin temperature level. With more pressure being included to the engine through the turbocharger, general temperature levels of the engine will likewise rise.
The warmer the consumption air, the less thick, and the less oxygen offered for the combustion event, which lowers volumetric effectiveness. Not only does excessive intake-air temperature decrease effectiveness, it also results in engine knock, or detonation, which is damaging to engines. To compensate for the boost in temperature, turbocharger units often make usage of an intercooler between succeeding stages of boost to cool off the intake air.
The Best Strategy To Use For Turbochargers
There are 2 areas on which intercoolers are typically installed. turbochargers. It can be either installed on top, parallel to the engine, or installed near the lower front of the automobile. Top-mount intercoolers setups will result in a decline in turbo lag, due in part by the area of the intercooler being much closer to the turbocharger outlet and throttle body.
Front-mount intercoolers can have the possible to provide better cooling compared to that of a top-mount. The area in which a top-mounted intercooler is situated, is near among the hottest areas of a cars and truck, right above the engine. This is why most manufacturers include large hood scoops to assist feed air to the intercooler while the car is moving, however while idle, the hood scoop provides little to no benefit.
With more distance to take a trip, the air you can check here circulated through a front-mount intercooler may have more time to cool. Methanol/water injection has been around since the 1920s however was not made use of up until The second world war. Including the mix to intake of the turbocharged engines decreased operating temperatures and increased horse power.